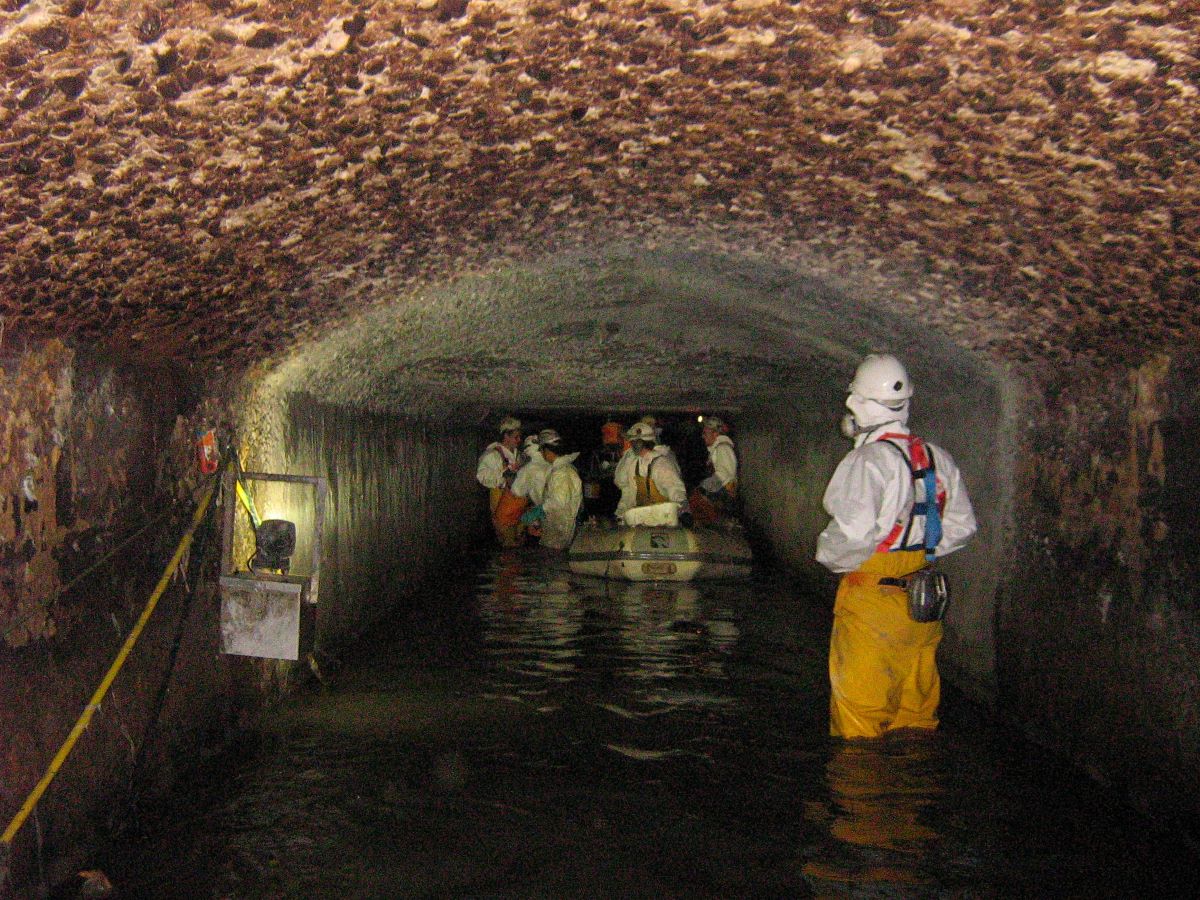
Infrastructure Maintenance: How Regular Inspections Can Prevent Costly Concrete Repairs
The durability and longevity of concrete infrastructure is essential for sustainable urban life. However, they face degradation from time, weather and use. This degradation can potentially compromise their integrity.
Regular inspections play a crucial role in mitigating these degradation challenges. Through proactive access and inspection, asset owners can detect early signs of deterioration and address emerging issues promptly.
Regular inspections can enable proactive and necessary repair work that can then ultimately extend the asset’s lifespan, reducing the cost of reactive repairs and enhancing reliability and safety.
Importance of Regular Inspections
1. Proactive Identification of Issues
It’s essential to detect and address concrete infrastructure issues before they escalate. Concrete, though durable, faces deterioration such as steel corrosion from moisture and salts, cracking due to thermal changes, chemical attacks and wear from loads.
Infrastructure managers and engineers should conduct scheduled inspections to carefully assess the condition of concrete structures, aiming to ensure their long-term functionality and safety.
These inspections involve thorough evaluations of critical parameters such as surface integrity, including checking for cracks, spalling or discolouration. These are indicators of underlying issues.
Evaluating structural stability is equally crucial, as it assesses the concrete’s ability to withstand operational loads and environmental stresses.
Advanced methodologies and equipment, such as LiDAR, photogrammetry and 3d mapping software, play a pivotal role in detecting internal defects that are not visible to the naked eye. This proactive approach ensures that infrastructure assets remain resilient and capable of serving communities effectively over their intended lifespan.
At Metrocorp, we invest in new methodologies and equipment like using drones for inspection work to ensure that we get the best information possible to help our partners identify actionable steps that can be taken when it comes to the infrastructures they own.
Early detection allows timely interventions. For example, identifying hairline cracks prompts sealant or coating applications. Monitoring corrosion in tunnels may lead to corrosion protection systems.
Proactive inspections prevent failures, optimise budgets and reduce downtime, ensuring continuous service to communities relying on infrastructure.
2. Components of Effective Inspection Programs
These help assess asset conditions, identify vulnerabilities and prioritise maintenance efforts and they include:
- Scheduled Inspections: Establishing regular, tailored inspection schedules based on structure type and usage.
- Comprehensive Assessment Criteria: Evaluating surface condition, structural integrity and environmental factors.
- Utilisation of Advanced Technologies: Employing drones and LiDAR scanners to name a few.
- Data Integration and Analysis: Using analytics for insights, risk assessment and resource allocation.
- Documentation and Reporting: Providing detailed reports to guide maintenance actions and ensure transparency.
3. Benefits of Proactive Maintenance
Proactive maintenance, supported by regular inspections and comprehensive assessments, offers significant benefits for concrete infrastructure:
- Prolonged Asset Lifespan: Early detection and intervention during inspections prevent minor issues like surface cracks or corrosion from progressing into severe structural defects, thereby extending the operational lifespan of assets.
- Improved Cost-effectiveness: Addressing small-scale issues through scheduled inspections incurs lower costs compared to emergency repairs triggered by structural failures. Proactive maintenance minimises downtime and optimises operational efficiency.
- Enhanced Safety and Reliability: Identifying potential hazards early, such as weakened structural components, ensures infrastructure safety and reliability. This mitigates risks of accidents and service disruptions, supporting community welfare and economic activities.
- Optimised Resource Allocation: Data-driven inspections prioritise maintenance actions based on risk assessment, efficiently allocating resources like labor, materials and equipment.
- Sustainability and Resilience: Proactive maintenance reduces environmental impact by extending infrastructure lifespan, minimising material consumption and enhancing community resilience against natural disasters.
Challenges and Solutions
Despite the clear advantages of proactive maintenance for concrete infrastructure, several challenges may hinder effective implementation. These challenges include budget constraints, limited access to advanced inspection technologies and the complexity of managing diverse infrastructure portfolios.
However, these challenges can be addressed through strategic planning, collaboration with specialised service providers and leveraging innovative solutions.
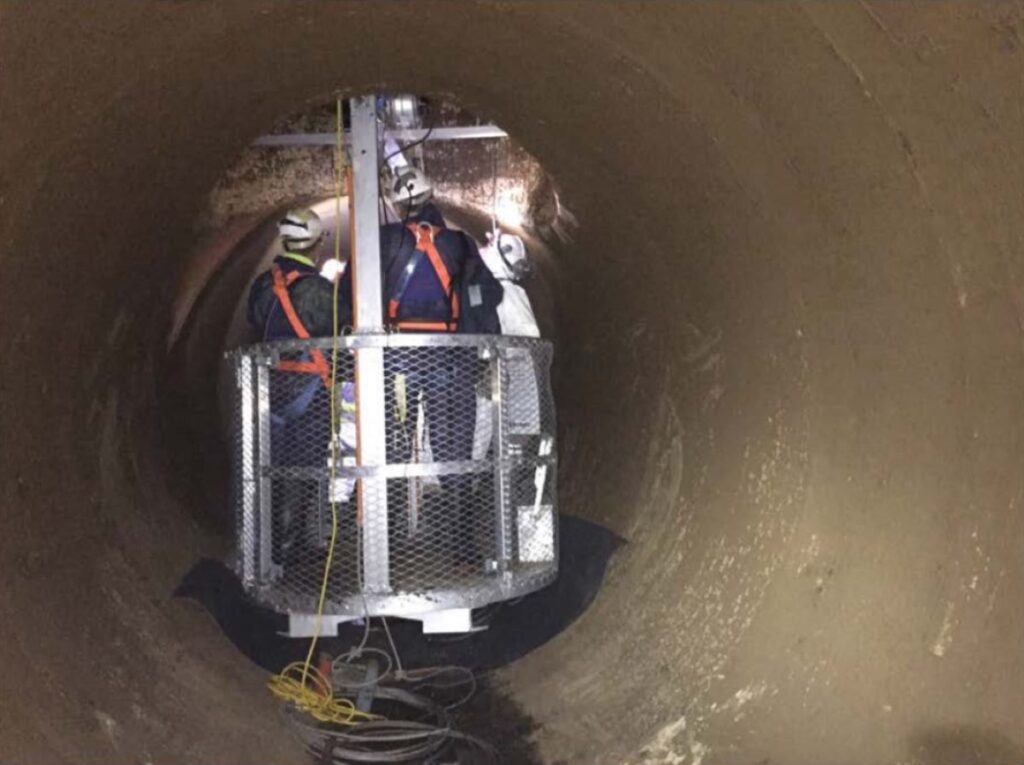
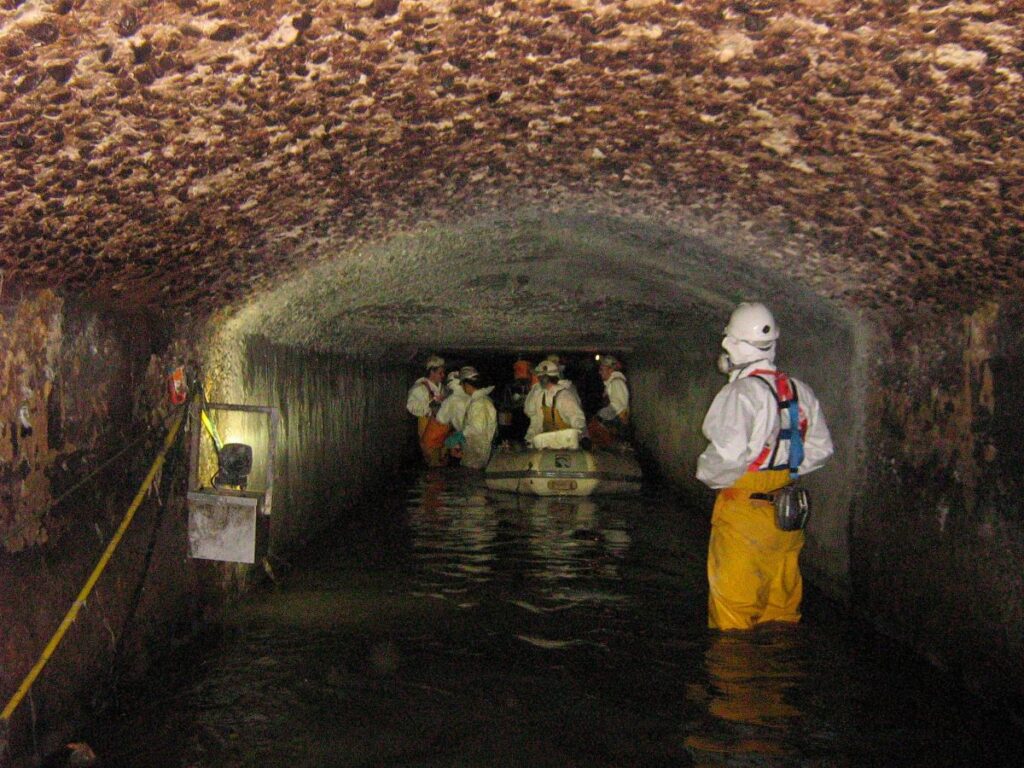
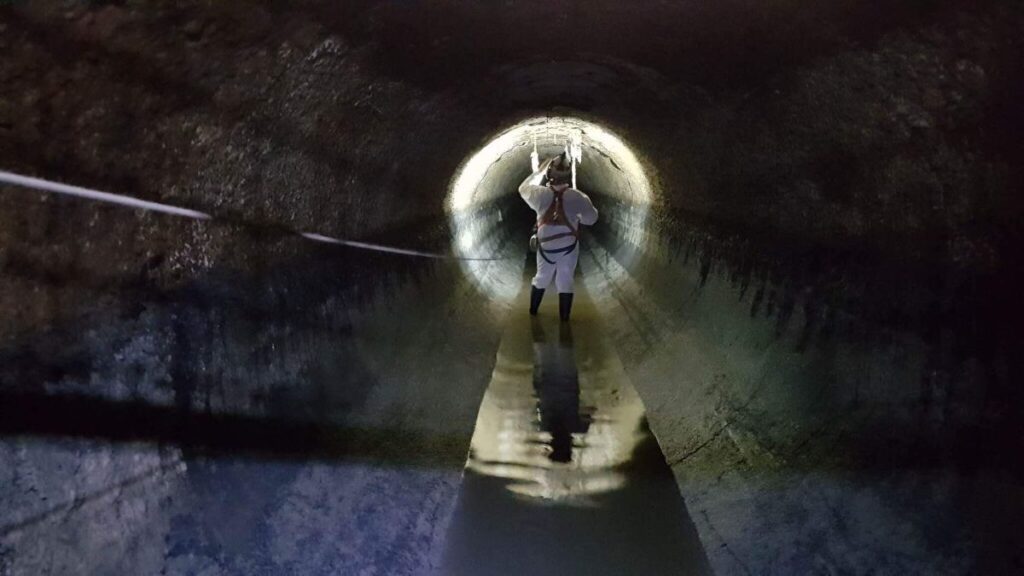
Conclusion
The importance of regular inspections and proactive maintenance cannot be overstated in preserving the integrity and functionality of concrete infrastructure. By identifying potential issues early, proactive maintenance strategies mitigate risks, reduce lifecycle costs and enhance safety and reliability.
Comprehensive assessment programs, supported by advanced technologies and data-driven analysis, empower infrastructure managers to make informed decisions and optimise resource allocation.
Embracing proactive access, inspect and repair practices remains essential for sustainable urban development and resilient infrastructure systems.
By prioritising preventive measures over reactive repairs, infrastructure asset owners and managers can contribute to building safer, more efficient and durable infrastructure.