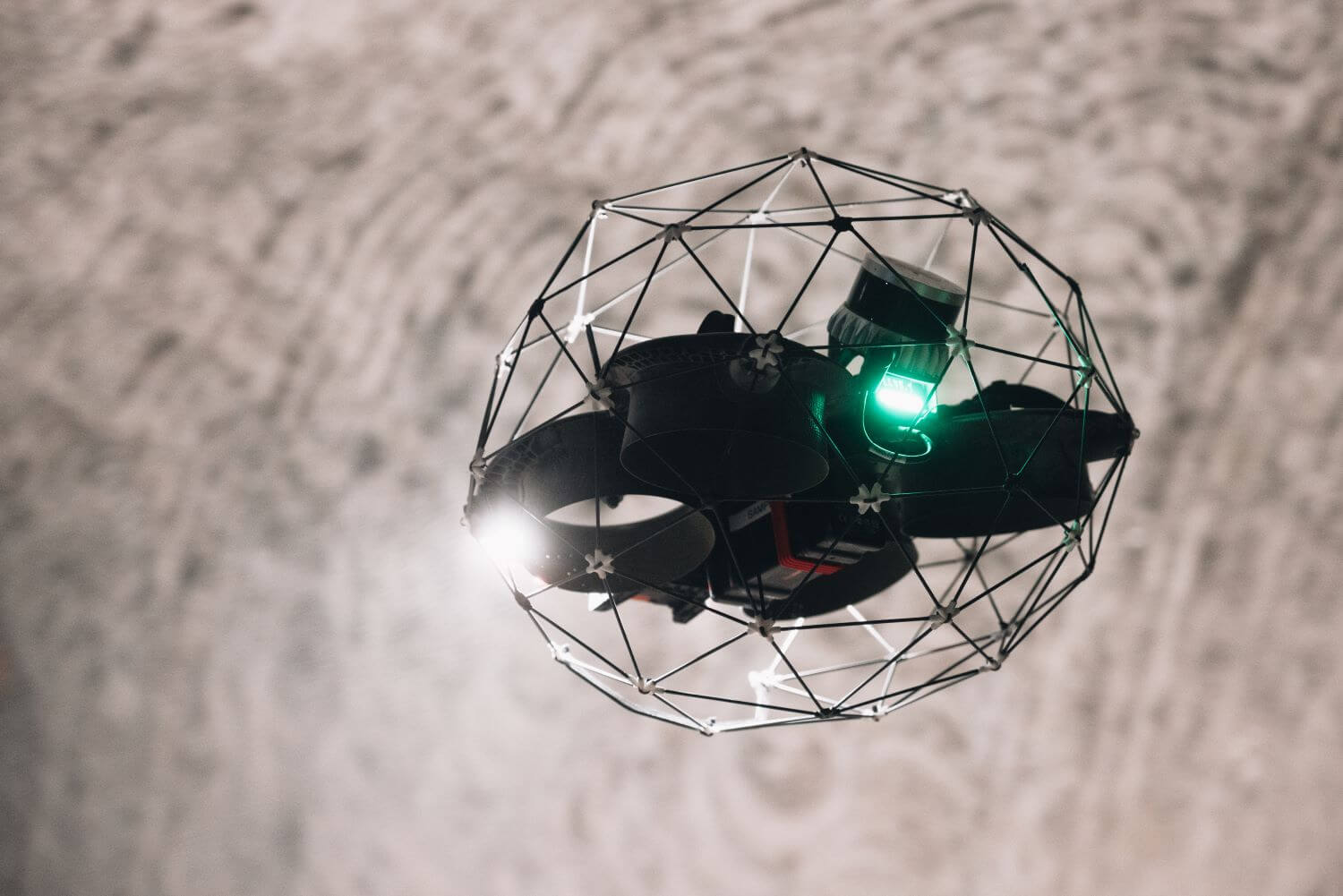
Enhancing Safety and Efficiency in Hazardous and Confined Space Inspections Through Drone Technology
Project Details
Hazardous and confined space inspections, especially in infrastructure like tunnels, reservoirs, and sewers, pose significant risks. These environments are often characterised by limited access, poor ventilation and the presence of hazardous substances, which can lead to several dangers.
In confined spaces, the air quality can be severely compromised due to inadequate ventilation, leading to low oxygen levels that can cause asphyxiation. Additionally, the buildup of toxic gases, such as methane, hydrogen sulfide or carbon monoxide, is a critical hazard.
Structural integrity is another concern. Aging infrastructure can have weakened or deteriorating concrete, increasing the risk of collapses or falls. Inspectors may also face physical constraints, making it challenging to manoeuvre or exit quickly in an emergency.
Furthermore, the presence of water and waste in sewers and similar structures adds the risk of contamination and disease exposure.
Electrical hazards also pose a threat, especially in tunnels with lighting or machinery. Accidental contact with live wires or malfunctioning equipment can result in electrocution.
Hazardous and confined spaces are challenging to access, inspect and repair, but with investments in drone technology, Metrocorp has been able to make the access and inspection processes significantly more efficient, effective and most importantly much safer.
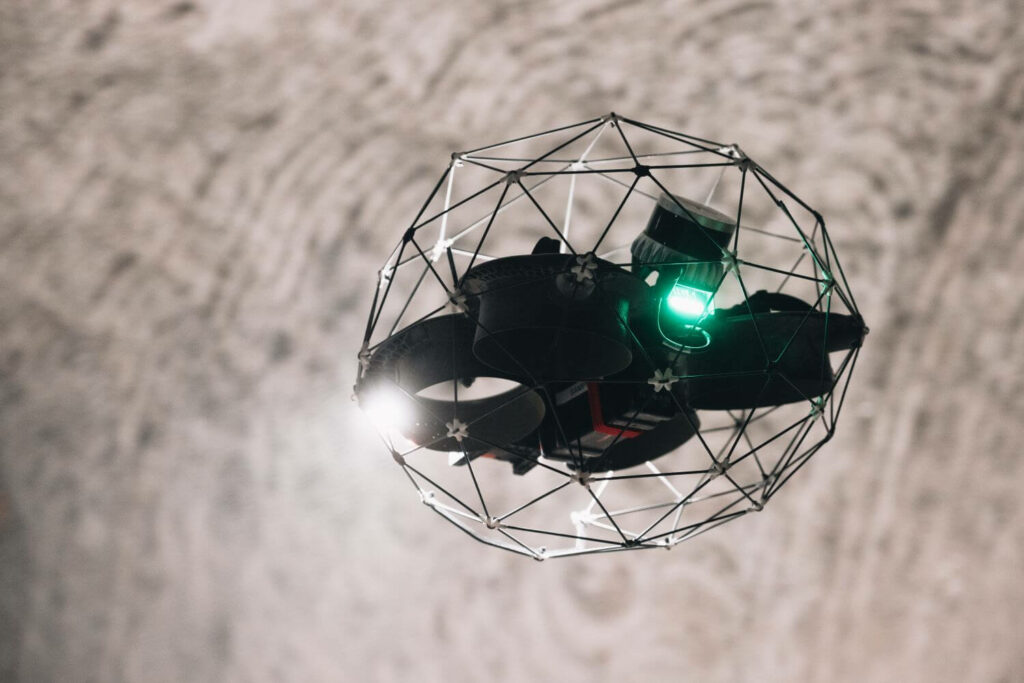
The Challenge
One of our client’s water tunnels located north of Sydney required urgent inspection.
Preliminary assessments by a team, including a geotechnical and structural engineer, deemed some sections of the tunnel unsafe due to risks of rock falls and water leaks. Compounding these risks were metal cages used to barricade some sections of the tunnel that were left there form previous work.
Access to the tunnel, although it was not entirely impossible, was high-risk, and safety concerns were paramount.
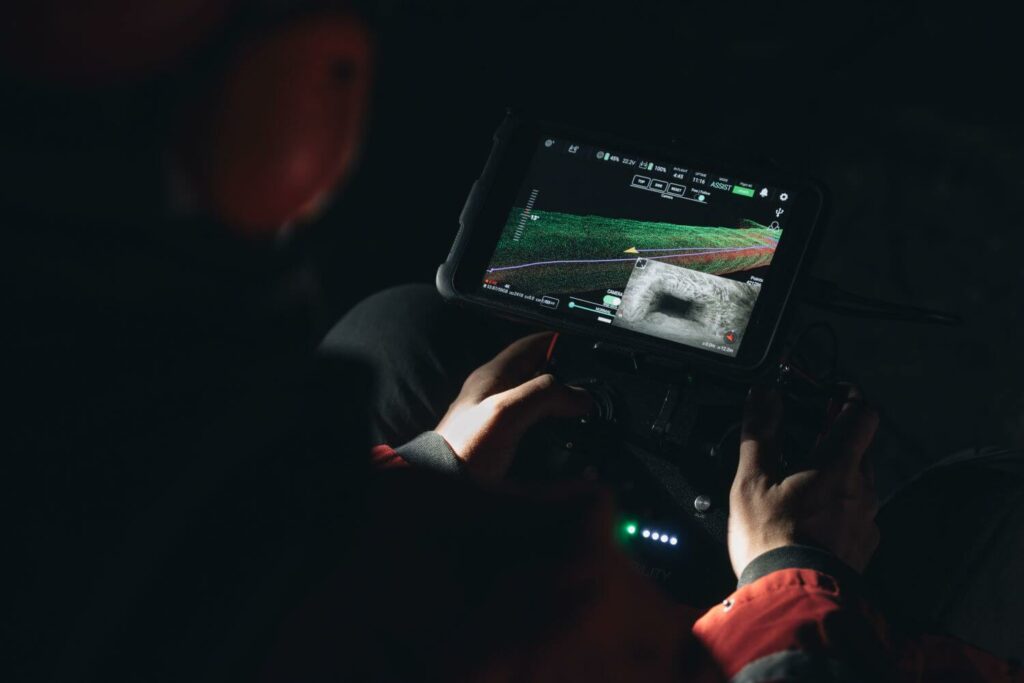
What We Did
To overcome the hazards of manual inspection and to bring the inspection process up-to-date swiftly and safely, the decision was made to deploy drone technology to gain safe access and inspect the tunnel.
This approach allowed for detailed data capture using high-resolution photography and 3D modelling. We also completed comprehensive scans of the tunnel to evaluate its structural integrity. This was achieved without human entry and enabled efficient and effective data collection that could not be achieved through traditional inspection methods.
The drone operation was meticulously planned and executed by our trained drone team, which managed to overcome challenges such as debris interference and signal issues.
Adjustments were made to the flight plan on the fly, ensuring comprehensive coverage and data collection.
This remote method of inspection provided detailed visual and structural data, which was then used to generate reports on the tunnel’s condition and plan the remediation that was well overdue.
The Results
By utilising the drone, we were able to mitigate safety risks as the technology eliminated the need for human presence in hazardous areas.
We also saw an improvement in overall efficiency as drone inspections were completed more quickly than manual inspections would have been, accelerating the decision-making process for necessary repairs.
Utilising the technology was cost-effective as well. It reduced preliminary work such as obtaining several approvals, which are typically required for manned inspections.
And of course, we benefited from the enhanced quality of data collected, providing the client with a detailed understanding of the tunnel’s condition and facilitating more informed maintenance and repair decisions.
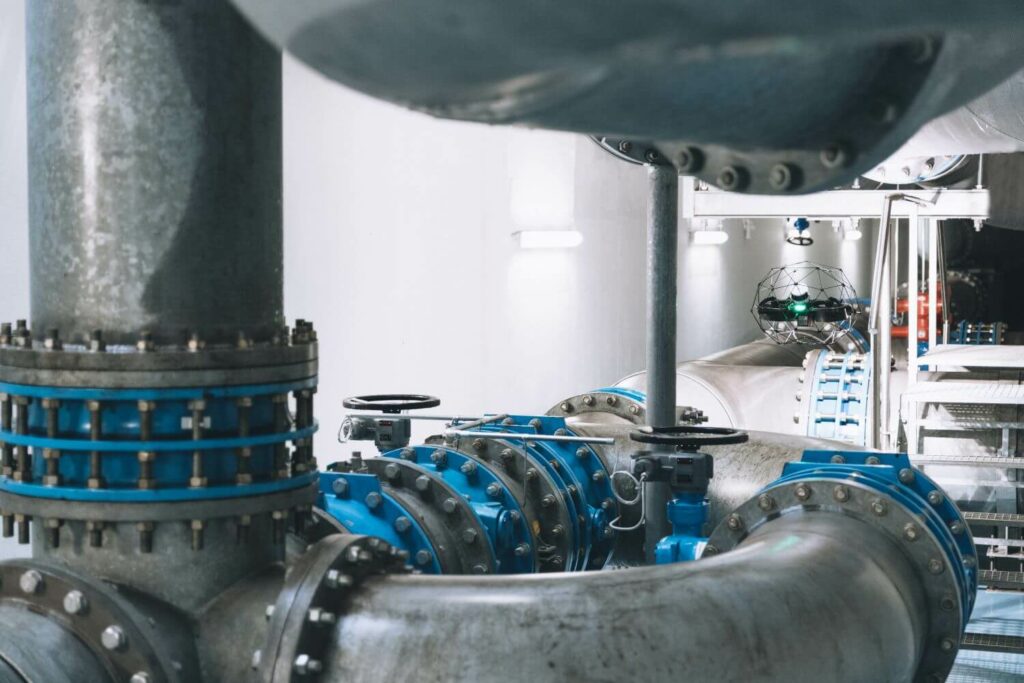