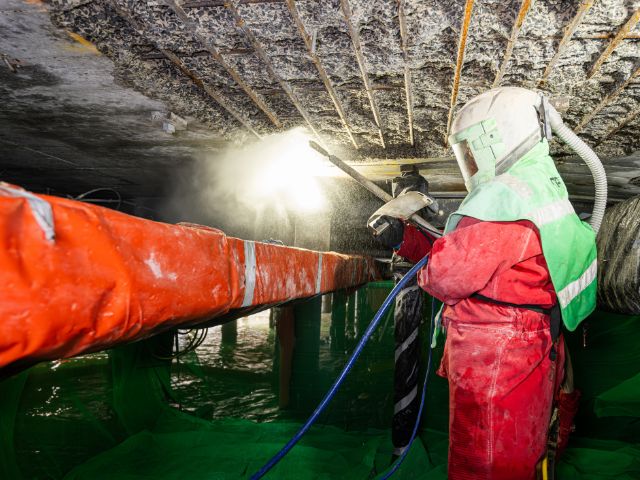
Understanding the Complexities of Concrete Repair and Protective Coatings
Introduction
Concrete is fundamental to modern infrastructure, forming the literal base for our tunnels, roads and bridges. However, despite its strength and durability, concrete is susceptible to a range of environmental and structural stresses that can degrade its quality and shorten its lifespan.
This blog aims to demystify the processes of concrete repair and protective coatings, and the critical maintenance practices we follow.
Challenges in Maintaining Concrete Structures
There are plenty of challenges that come with concrete structure maintenance, one of which is the corrosion of steel reinforcements within the concrete slabs. Internal issues may persist long before visible signs appear on the concrete.
Environmental aggressors such as moisture, salt and chemicals can accelerate this corrosion and further damage the concrete. Additionally, everyday structural stresses from heavy usage and loads can cause micro-cracks that gradually worsen if not addressed.
The technical complexities involved in diagnosing and repairing these issues require advanced expertise and often sophisticated technology. Because they are demanding and often difficult to perform, they call for professionals who have first-hand experience and successes in addressing and repairing infrastructure assets.
Common Concrete Issues
Concrete structures commonly exhibit several types of distress that can lead to serious damage if not remedied.
Cracks, which may appear trivial, are often the first sign of stress and can lead to severe structural problems if they allow moisture or harmful chemicals to penetrate deeper into the concrete.
When the surface layer flakes off (spalling) or separates from the underlying material (delamination) this will not only affect the surface of the concrete but also compromise the structural integrity of deeper layers.
Spalling and delamination are more than just surface issues; they indicate deeper structural problems within the concrete and may expose the inner layers to environmental elements, accelerating deterioration.
This exposure can lead to further weakening of the concrete’s internal structure, potentially compromising the load-bearing capacity and overall stability of the entire structure if not addressed promptly.
Chemical attacks from industrial activities can alter the chemical composition of concrete, weakening it and making it more susceptible to other forms of damage.
Industrial activities that create a risk of chemical attacks on concrete include processes that involve the use or production of harsh chemicals, such as manufacturing plants, chemical processing facilities and wastewater treatment plants.
In these environments, acids, alkalis, sulphates and chlorides are commonly present and can penetrate the concrete, altering its chemical composition.
For example, spills or leaks from storage tanks, pipelines or equipment can introduce these corrosive substances to the concrete, leading to degradation and making it more vulnerable to further damage like cracking, spalling and corrosion of embedded steel.
Chemical attacks occur when aggressive substances, such as acids, sulphates or chlorides, penetrate the concrete and react with its components, leading to a breakdown of the material’s internal structure. This can weaken the concrete significantly, making it more susceptible to cracking and spalling.
Carbonation, on the other hand, is a process where carbon dioxide from the air reacts with the calcium hydroxide in the concrete, lowering its pH and making the embedded steel reinforcement more prone to corrosion, which can ultimately compromise the structural integrity of the concrete.
Concrete Repair Techniques
Repairing concrete is an art that requires a deep understanding of the material’s properties.
Repairs start with careful surface preparation and involves cleaning the concrete, removing loose material and sometimes reshaping the surface to allow for better adhesion of repair materials.
To understand how Metrocorp has continued to bring innovation to surface preparation, read our case study on Ultra High Pressure cleaning.
Techniques such as patching and resurfacing are used to address both aesthetic and structural issues, restoring the concrete’s original appearance and strength.
Crack injection is a specialised repair technique that fills cracks with a sealant, preventing further deterioration and restoring structural integrity.
Protective Coatings for Concrete
Protective coatings play a dual role in not only restoring the appearance of concrete but also in providing a barrier against environmental and chemical damages.
These coatings are designed to prevent water, chemicals and physical impacts from reaching the concrete, thus prolonging its lifespan.
The choice of coating—be it epoxy, polyurethane, or another material—depends on the specific conditions and requirements of the structure.
Epoxy coatings are commonly used in concrete repair when there is a need for strong adhesion and chemical resistance. They are ideal for environments where the concrete is exposed to harsh chemicals, such as in industrial settings or wastewater facilities, because they form a hard, durable surface that can withstand significant wear and chemical exposure.
Polyurethane coatings are preferred in situations where flexibility and impact resistance are crucial. They are often used in areas subject to heavy traffic or frequent movement, such as parking garages and bridges, because they can absorb impacts and accommodate the expansion and contraction of concrete without cracking.
Other materials, like acrylic coatings, are used when UV resistance and aesthetic considerations are important. These coatings are typically applied to exterior surfaces, where protecting the concrete from sunlight and maintaining an attractive appearance are priorities.
Each material is chosen based on the specific environmental conditions, the type of concrete structure and the desired balance between protection and flexibility.
Proper application is critical and can involve various techniques, each suited to different types of coatings and environmental conditions.
Different application methods for concrete coatings include roller application, spray application and trowel application, each chosen based on the type of coating and the specific environmental conditions.
Roller application is often used for smaller areas or when a thicker, more controlled coating layer is required, providing precision in coverage.
Spray application is ideal for large or complex surfaces where a uniform, thin layer is needed, allowing for quick coverage and consistent results across expansive areas.
Trowel application, typically used for specialised coatings, allows for precise control over the thickness and finish, making it suitable for areas that need detailed or textured surfaces.
Coatings simplify maintenance and cleaning by creating a smooth, non-porous surface that resists the absorption of water, chemicals and dirt, making it easier to remove contaminants and prevent stains.
This protective layer reduces the need for frequent deep cleaning and helps prevent the buildup of grime or biological growth, such as mold or algae. Additionally, coatings minimise surface wear and tear, ensuring that the concrete remains in good condition with less frequent maintenance interventions.
Factors Affecting Repair and Coating Success
The success of concrete repairs and the effectiveness of protective coatings are influenced by environmental conditions such as temperature and humidity. Additionally, because of their impact on the curing process and the final properties of the materials used, the condition of the concrete at the time of repair plays a crucial role.
Substrates damage or contaminate surfaces hindering the effectiveness of repairs by preventing proper adhesion of repair materials or coatings. When the substrate is cracked, weakened or contaminated with substances like oil, dirt or chemicals, it can lead to poor bonding, resulting in repairs that fail prematurely.
Proper surface preparation is essential to remove these contaminants and ensure a clean, stable base for successful repair and coating application.
Additionally, the skill with which repairs and coatings are applied is paramount to ensuring their durability and effectiveness. The skill level of the professionals applying repairs and coatings is crucial because even the best materials can fail if not applied correctly.
Precise application techniques ensure that repair materials bond properly to the substrate, creating a seamless integration that restores structural integrity. Moreover, the correct application of protective coatings, including factors like thickness, curing times and environmental conditions during application, determines their ability to shield the concrete from further damage.
Inadequate application can lead to issues such as uneven coverage, poor adhesion or insufficient protection, ultimately compromising the longevity and effectiveness of the repair.
Emerging Technologies in Concrete Protection
The field of concrete protection is rapidly advancing, with new technologies enhancing the effectiveness of traditional methods.
Advanced materials like polyurea provide rapid curing times and exceptional durability.
Developments in moisture-cured urethanes and multi-functional coatings offer solutions tailored to specific environmental challenges, providing more robust and long-lasting protection.
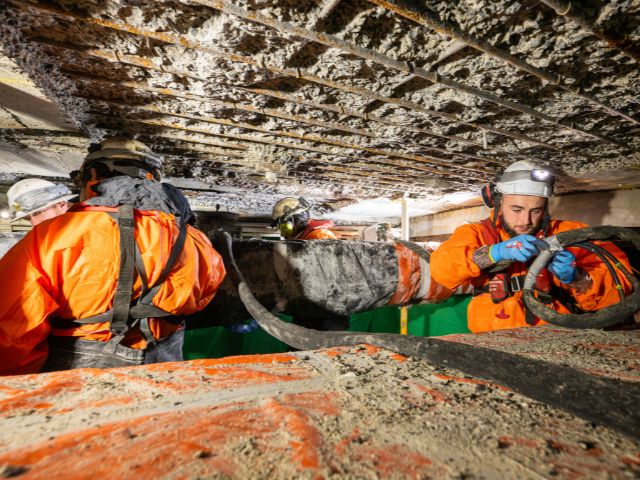
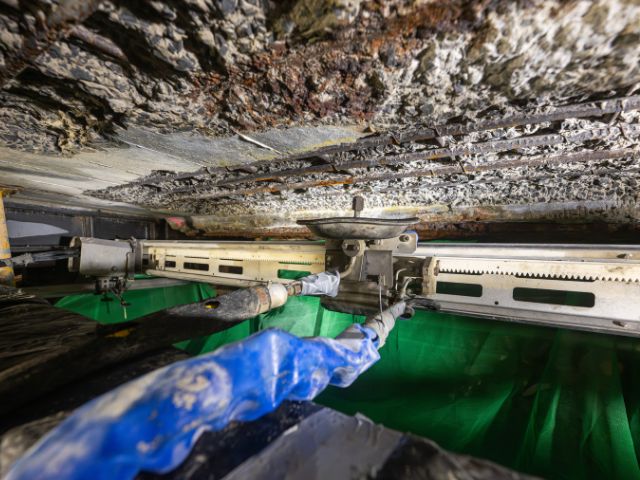
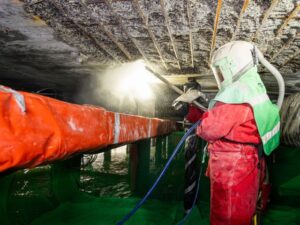
Conclusion
Understanding and implementing concrete repair and protective coatings are crucial for maintaining the longevity and safety of infrastructure.
With the right knowledge and technologies, the lifespan of concrete structures can be significantly extended, ensuring they remain safe and functional for future generations.
To ensure the longevity of your concrete assets, consider consulting with experts who can provide tailored solutions based on the latest technologies and techniques.
Don’t wait for the damage to become irreversible—proactive measures are key to maintaining the integrity and functionality of your infrastructure.